01 No draft angle added
A draft angle is required in the mold to release plastic parts from the mold. Plastic typically shrinks toward the center of the part. Without a draft angle, the part will stick to the mold and cannot be properly demolded. If possible, design a 1° draft angle on each side; any draft angle will help release the part.
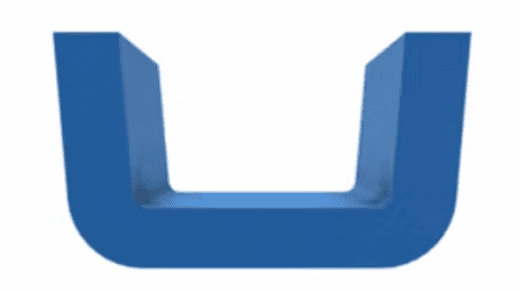
02 Uneven wall thickness
Different wall cross-sections are common in part design and can lead to unexpected part characteristics during molding. Plastic has difficulty flowing and transitioning between uneven wall thicknesses. Thicker wall sections experience different shrinkage, which may cause part deformation. Aim for wall thicknesses that are at least thicker in the gate area and thinner toward the end of filling. Strive for wall thicknesses of 0.080–0.120 inches and utilize rib and corner support features in part design.
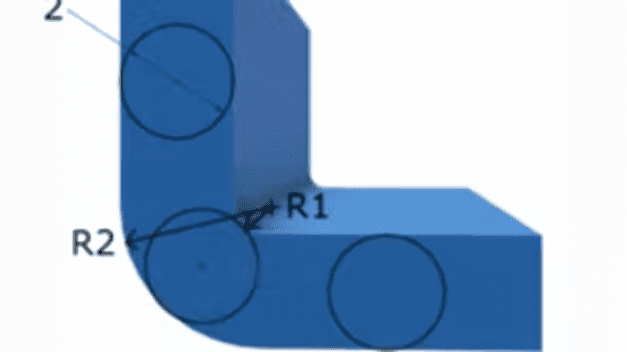
03 Unnecessary recesses
Due to the complexity of modern part designs, undercuts are often designed but overlooked. Undercuts in the mold must be addressed before part removal, otherwise they will damage the part. During mold design, there are many methods to address undercuts, such as through-core designs, slides, cores, or lifters. A simple design rule: undercut + complex mold = higher cost.
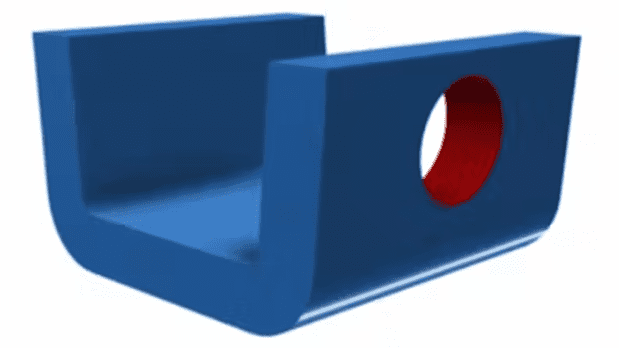
04 Incorrect material selection
Material selection is another common mistake I encounter. Material selection should be based on the part’s location. Parts exposed to outdoor conditions should contain UV stabilizers to prevent cracking. Parts subjected to loads should include reinforcing fillers such as glass fiber. Parts with bearing surfaces should incorporate additives like lubricants.
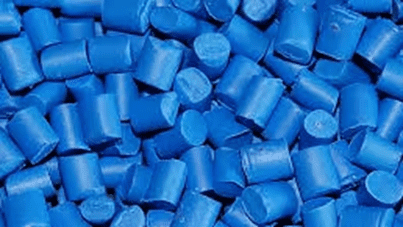
05 Lack of radius on corners
In part design, corner radii are often overlooked. Corner radii strengthen the area, making it more durable over time. The radius reduces stress concentration and fracture in plastic parts. It also makes the part look more aesthetically pleasing and reduces the risk of injury during handling.
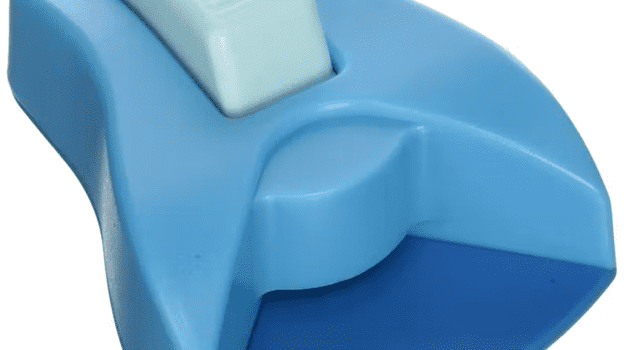