What is surface roughness?
Surface roughness is a measurement of the average texture of a part’s surface, specifically referring to the surface roughness after CNC machining. Various parameters are used to define surface roughness, with Ra (average roughness) being the most common. Ra is calculated by measuring the difference between the height and depth of surface features. When measured under a microscope, Ra is typically quantified in micrometers. It is important to note that surface roughness and surface finish are two distinct concepts. While surface finish can be improved through finishing techniques such as anodizing, sandblasting, and electroplating, surface roughness specifically refers to the surface texture of a part immediately after machining.
How can different surface roughness values be achieved?
Typically, the surface roughness of a part after machining is not randomly generated but is carefully planned and controlled to meet specific standards. This means that surface roughness values are predefined. However, this does not mean that any value can be arbitrarily specified. In the manufacturing industry, there are a series of widely accepted Ra value standards, such as those specified in ISO 4287, which can be explicitly specified during CNC machining.
These standard values range widely, from 25 microns to 0.025 microns, to meet the needs of different manufacturing and post-processing operations.
We offer four surface roughness grades, which are also typical specified values for CNC machining applications:
- 3.2 μm Ra
- 1.6 μm Ra
- 0.8 μm Ra
- 0.4 μm Ra
Different applications have different requirements for surface roughness. Lower surface roughness values are only specified under specific conditions. This is because lower Ra values require additional machining operations and stricter quality control, which inevitably increase processing costs and time. Therefore, post-processing operations are generally not preferred when specific surface roughness is required, as these operations are difficult to control precisely and may adversely affect part dimensional tolerances.

In certain applications, surface roughness significantly impacts the functionality, performance, and durability of parts. It directly influences factors such as friction coefficients, noise levels, wear rates, heat generation, and adhesion during use. The importance of these factors varies depending on the specific application scenario. Therefore, while surface roughness may not appear critical in some cases, it plays a crucial role in many others. These applications include, but are not limited to, high-tension, high-stress, and high-vibration environments; components requiring precise fit and smooth movement; rapidly rotating parts; and medical implants. As mentioned earlier, different applications have distinct and stringent requirements for surface roughness.
The following section introduces the roughness grades offered by Debaolong Seiko and provides all the information needed to select the appropriate Ra value for your application.
→ 3.2 μm Ra
This is the standard commercial machine surface finish. It is suitable for most consumer parts, sufficiently smooth but with visible machining marks. Unless otherwise specified, this surface roughness is used by default.
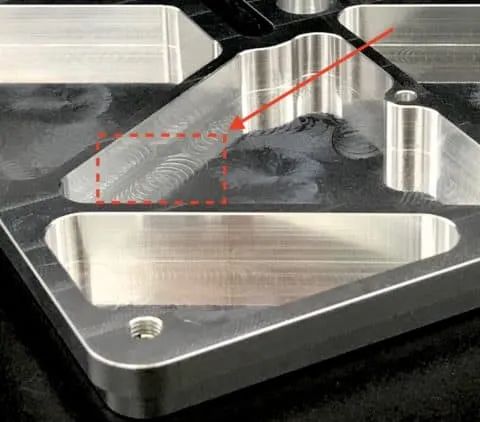
→ 3.2 μm Ra machining surface roughness
3.2 μm Ra is the maximum surface roughness recommended for parts subjected to stress, load, and vibration. It can also be used for mating surfaces on moving parts when the load is light and the movement is slow. Machining should be performed at high speed, with fine feed rates and light cutting.
→ 1.6 μm Ra
Under normal conditions, this option will result in only slight visible cutting marks. This Ra value is recommended for close-fitting and load-bearing parts, and is sufficient for surfaces with slow movement and light loads. However, it is not suitable for rapidly rotating components or those subjected to severe vibration. This surface roughness is achieved under controlled conditions through high-speed, fine feed, and light cutting.
Price: For standard aluminum alloys (e.g., 3.1645), this option increases production costs by approximately 2.5%. Costs increase with the complexity of the part.
→ 0.8 μm Ra
This surface finish is considered high-grade and requires strict control during production, resulting in higher costs. It is recommended for parts subject to stress concentration. It can be used for bearings when movement is occasional and loads are light.
Price: For standard aluminum alloys (e.g., 3.1645), this option increases production costs by approximately 5%. As part complexity increases, prices also increase.
→ 0.4 μm Ra
This surface roughness achieves a finer level (technically referred to as “smoother”), representing very high-quality surface finishing. It is particularly suitable for parts subjected to high tension or stress, as well as fast-rotating components such as bearings and shafts. Due to the more complex manufacturing processes required to achieve this surface roughness, it is only selected when smoothness is critical.
Price: For standard aluminum alloys (e.g., 3.1645), this option increases production costs by approximately 11–15%. The price increases further with the complexity of the part.