Over the past few decades, the significant advancements in additive manufacturing technology have transformed the potential ways in which products are designed, developed, manufactured, processed, and distributed. The automotive industry has been particularly proactive in experimenting with 3D printing, and these advancements have opened new doors in multiple areas. This article provides an overview of current developments and highlights how 3D printing is reshaping the automotive sector.
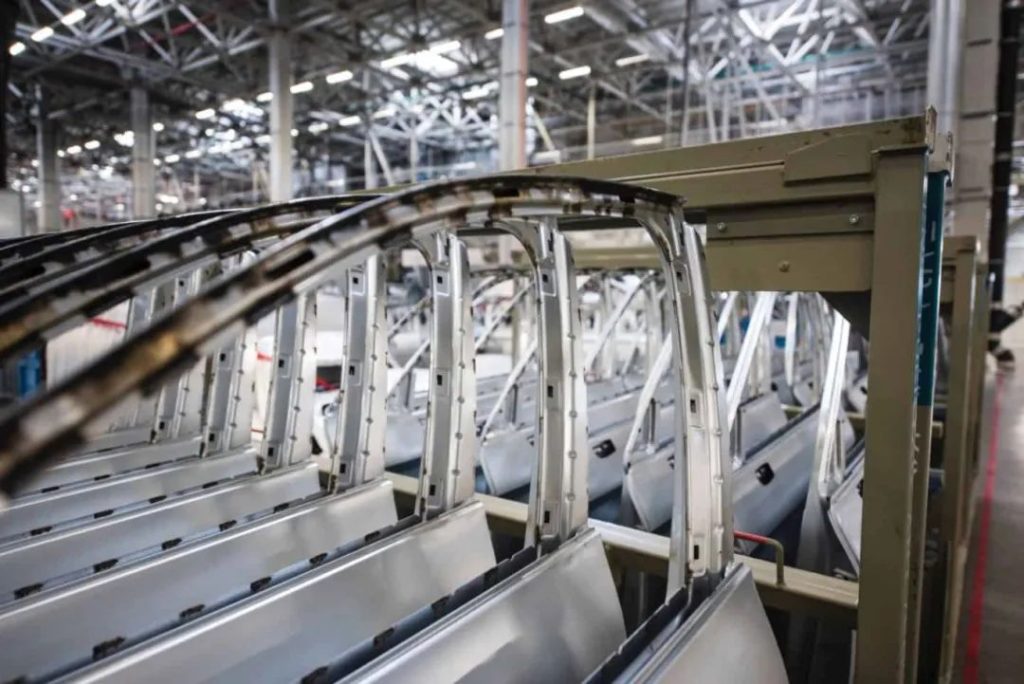
In which fields does 3D printing have significant advantages?
The transition from traditional manufacturing processes to 3D printing technology has enabled companies in various industries to achieve revolutionary improvements in the technology and commercial aspects of components and products. However, in the automotive field, additive manufacturing will have a more profound impact on two main aspects.
Product innovation
Additive manufacturing can produce components that are difficult to manufacture using traditional methods, with fewer design constraints. This design flexibility opens up possibilities for innovation, such as adding improved features like integrated electrical wiring through hollow structures, weight reduction through lattice structures, and complex geometries that are impossible to achieve with traditional processes. Additionally, new additive manufacturing technologies are increasingly capable of producing multi-material printed components with unique properties, such as electrical conductivity and variable strength. These additive manufacturing processes play a crucial role in creating safer, lighter, faster, and more efficient vehicles of the future.
Supply Chain
Additive manufacturing effectively shortens overall delivery times by eliminating the need for new tools and producing finished products directly. In addition, since additive manufacturing typically uses only the materials required to produce parts, it can significantly reduce waste and lower material usage. Furthermore, the lightweight components produced by additive manufacturing can reduce handling costs, while on-demand and on-site production help lower inventory costs and provide flexible supply chain solutions. Additive manufacturing supports decentralized production at low to medium volumes, enabling cost reductions and enhancing the ability to produce products closer to customer locations, thereby reducing supply chain complexity.
Product stages where additive manufacturing can be applied
Additive manufacturing, with its unique advantages, can replace several processes in traditional automotive production. Here are four important changes that additive manufacturing can bring to the automotive industry.
Prototyping process
The prototyping process typically requires a significant investment of time and money, especially as the number of product iterations increases. Rapid prototyping (3D printing) enables companies to quickly turn initial ideas into compelling proof-of-concept models. These concepts can then be further developed into highly accurate prototypes that closely resemble the final product, guiding the product through a series of iterative and validation stages toward mass production. In the automotive industry, rapid validation is critical. With 3D printing technology, highly realistic and representative prototypes can be produced in a matter of days, significantly reducing costs and shortening the time from concept to final product, thereby enhancing the overall product development workflow.
Maintenance and Support (Spare Parts)
With computer-aided design (CAD), nearly all components can be designed and stored as digital copies on a computer hard drive, eliminating the need for inventory maintenance. Using 3D printing technology, spare parts can be produced on demand. The accessibility of this technology will encourage suppliers to develop new service areas to provide convenient 3D-printed components and spare parts. Even reverse engineering based on digital scans can be used to remanufacture parts that are no longer in production. This technology can also breathe new life into outdated designs while easily replicating spare parts for classic models.
Customization
Customized production is costly and time-consuming in traditional manufacturing processes. However, 3D printing is well-suited for producing low-cost customized parts, offering manufacturers new production capabilities and enabling them to provide customers with customized products. For small custom car shops, using 3D-printed car parts not only enhances work quality and creativity but also provides ample room for experimentation and refinement of customized designs.
Continuous production (assembly of various components)
3D printing can enhance efficiency in the general component manufacturing stage. For example, what might have required assembling five or six automotive components can now be achieved with a single printed part. While individual components may be more expensive, this approach saves assembly time and costs. By merging components, 3D printing also helps reduce weight and improve fuel efficiency. From a production efficiency perspective, further applying 3D printing technology to general component manufacturing is highly rational.
Which technologies and materials are suitable?
From plastic decorative parts to metal engine components, additive manufacturing has proven its value and still has more potential to be tapped in terms of technical processes and available materials. The table below provides a brief overview of some popular options.
Application | Process | Material | Characteristics | Examples |
---|---|---|---|---|
Interior and Seats | SLA, SLS, MJF | Polymer | Customized decorative components | Instrument panel, seat frame |
Tires, Wheels, Suspension | SLS, MJF, SLM | Aluminum alloy, Polymer | Sturdy and durable components | Suspension spring, wheel cover |
Electronic Equipment | SLS, MJF | Polymer | Precision components | Sensor, single – component control panel |
Exhaust and Emission | SLM | Aluminum alloy, Polymer | Hollow metal parts | Cooling vent |
Under the Hood | SLS, MJF | Nylon | Heat – resistant functional components | Battery cover |
Lighting | SLA, MJF | Resin | Completely transparent, high – detail | Headlight, headlight prototype |
Air Duct | SLS, MJF | Nylon | Flexible ducts | HVAC ducts |
Prototype | SLA | Polymer | High clarity, clear details | High – clarity prototype |
Functional Mounting Brackets | SLS, SLM, MJF | Nylon 12, Titanium | Lightweight, high – strength | Generator bracket |
Complex Engine Components | SLM | Aluminum alloy | Integrated, lightweight, functional metal components | Wishbone suspension |
Industry Application Examples
Many automotive OEMs have begun using additive manufacturing, recognizing its capabilities and efficiencies, and here are two examples of applications.
Michelin launches 3D printed Uptis tires
French tire manufacturer Michelin launched its first additive manufacturing technology-enabled prototype tires in 2019 under the name Uptis (Unique Puncture Resistant Tire System) These tires are designed to require no inflation to reduce the risk of air leaks and other failures due to punctures or road obstacles. This design is possible solely thanks to additive manufacturing technology. If successful, the Uptis are expected to be fitted to a number of vehicles by 2024. In addition, these puncture-proof tires will reduce waste and promote sustainable transportation (one of the goals of the company’s Future Mobility Vision).
Porsche and the first 3D printed engine pistons
For the first time, automotive giant Porsche is using 3D printing technology to manufacture engine pistons. These additively manufactured parts are designed specifically for the high-performance engine of the Porsche 911 GT2. The 3D printing technology allowed the pistons to be optimized, making this critical engine component 10 percent lighter than conventionally manufactured pistons. Porsche used a specialized aluminum alloy to manufacture the pistons, resulting in performance that is better suited to this specific application.
Conclusion
Considering the wide range of capabilities opened up by additive manufacturing, automotive company leaders should consider utilizing additive manufacturing technologies to maintain a competitive edge. While traditional manufacturing techniques are deeply entrenched and will continue to dominate the automotive industry, additive manufacturing is gradually entering the field. Debaolong Seiko is currently working with the automotive industry to streamline their supply chain and dynamically expand their manufacturing capabilities in the areas of 3D printing and CNC parts.